Ice Dams
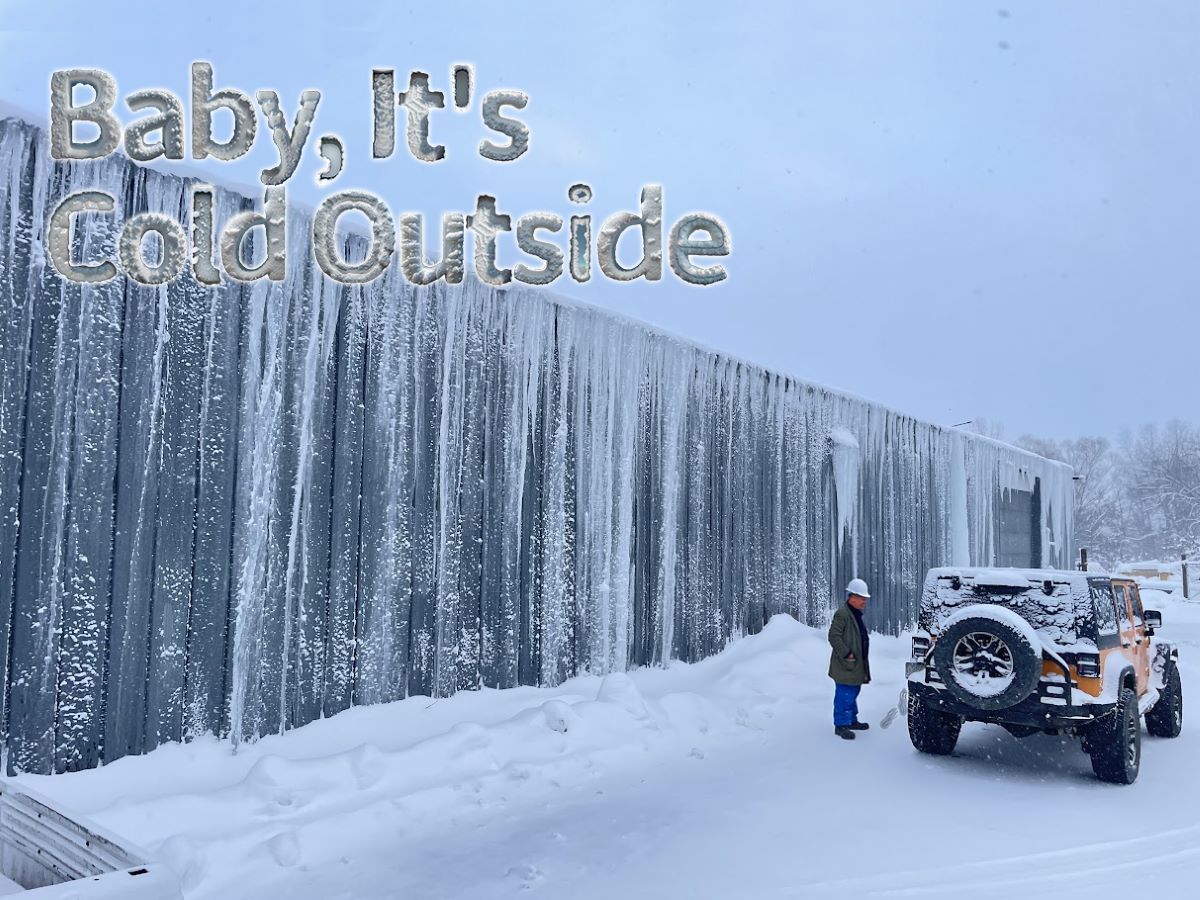
Ice Dams | Pre Engineered Steel Buildings
Pre-engineered steel buildings. What a delicious combination of engineering, cost efficiency, speed, and construction. And they’re typically one-third the cost of a conventional structure. With all those wonderful advantages, like the ingredients of a decadent cake – after indulging, there can be some real dynamic side effects that we’re not expecting. I never expected eating birthday cake at 2:30 am could lead to pre-diabetic sleep apnea. But that’s a different story. This story is about how to prevent ice dams from forming on the roofs of pre-engineered steel buildings.
These buildings are wonderful structures due to their adaptability for any business, from a tire repair shop to rocket engine manufacturing. The key component to all of these buildings is – like many things in the name pre-engineered. Every nut, bolt, column, beam, purlin, girt, service door, overhead door, etc., all fall within the context of being pre-engineered. Everything fits together. And like a LEGO set, if you follow the directions, the outcome is truly sensational. An aesthetically pleasing, cost-effective, multi-use structure that allows you to add on without any consequence to disrupting the prior engineered portion of the building.
The Realities of Ice Dams
Over a 40-year period, I watched a small building near Michigan’s West Coast go from a motorcycle repair shop to a pool installation company and then, finally, to a small non-denominational church. It’s amazing what a little paint and inspiration can do to a pre-engineered steel building. Each time the building was reoccupied, it was as though this pumpkin had become a new carriage in search of a princess who was missing a slipper.
However, with each iteration, every winter this building became a small ice castle. From the roof eave edge to the ground, columns of ice up to two or three feet in diameter – formed a sheet extending down the entire length of both sides of the building. I suspected these ice dams had something to do with the reimagining of this building several times. It also made me believe that these ice dams most likely contributed to the regular change in ownership.
If you’ve ever been inside a pre-engineered building that has significant ice dams in the month of January, and our typical January thaw hits, a bucket brigade can hardly keep up with the amount of water pouring inside some of these buildings.
Melt and Shed Function | Heat Transfer
Recently, we installed our MR Multi-Ply® Roof System MR MULTI-PLY® Roof System on a church in my town. The building was donated to the church for all the right reasons. The building was filled with the many free offerings from their congregation. Mattresses, living room sets, pool tables, light fixtures galore, and enough dining room tables with scratches to start a small café. Unfortunately, many of these well-wishing gifts were ultimately of zero value after the winter of 2022.
Several significant snow storms dropped many feet of snow, and then just as quickly, the weather in January shot up into the 60s. This caused a rapid melting and shedding of the roof at its high point, which was prevented from successfully coming off due to the ice that had formed on the unheated portion of the roof. It essentially created a log jam of sorts - allowing three to four inches of liquid to form behind the ice dam.
Keeping in mind that metal roofs are designed to shed water and never to hold it, the amount of water coming in at the eve edge could be measured by the 55-gallon drums being emptied every hour. The water entering through the roof system also caused the insulation to quickly fill up and quite literally burst at the seams. This, in turn, compounded the problem as now additional heat loss oat the roof was occurring due to the wet and damaged insulation.
I think it would be wise to take one small step backward to get a better understanding of pre-engineered steel buildings in the mid and upper Midwest. The pre-engineered building is literally designed to be a warm roof. The roof purlins conduct heat through the entire system to the building exterior, which helps create a melt and shed scenario. However, if we lack proper ventilation as well as insulation, this warm roof becomes a hot mess. Pre-engineered steel buildings are designed not around the R factor but rather around the U factor, the coefficient of the heat, and how it’s transferred from the inside of the building to the exterior.
Proper Ventilation
Several simple things can take your pre-engineered nightmare in the middle of February and help it perform just like all conventional structures when it comes to snow and ice.
First, let’s look at the principles of conventional construction. Today, quantities of insulation are mandated to help reduce costs associated with wintertime heating. By simply balancing the heat being generated inside the building and distributing it uniformly across the roof line this slows the overheating of the purlin that transfers heat to the building exterior. Secondarily, that heat that sits just below the roof can be reused to help keep the building interior more comfortable for the workers/volunteers working within the building.
One of the greatest mysteries to me is that out of the tens of thousands of pre-engineered steel buildings, I’ve looked at over 40 years, perhaps one in 500 included the very necessary venting at the peak of the roof.
Some would say venting allows the heat that is generated to keep the building comfortable to go into wholesale loss by installing roof vents. Nothing could be further from the truth. By exhausting the moisture-laden heat, we’re actually preserving the physics that are in play during the design criteria of the building. Thus, we cool the underside slightly to slow the melt shed process. This, in turn, minimizes the opportunity for ice dams to form.
Conclusion:
By ventilating the excess heat buildup at the eve edge – redirecting the unused heat back down to the work area – AND by keeping our existing insulation dry and free of condensation, we’ve accomplished a comfortable workspace, a significant improvement in heating and cooling costs AND insulation that when dry, can perform to expectation.