Limitations of Membrane Roofing Systems – EPDM, TPO, PVC
The importance of using the correct type of roofing system cannot be understated. To ensure safety, the roofing material must be suitable for the intended use of the building. Understanding the limitations of EPDM, TPO, and PVC roofing systems will help you make the right choice for your building. This prevents accidents, including employee safety hazards like equipment damage, fire damage, and potential explosions.
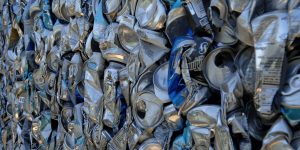
For example, during the scrap re-melting process in the aluminum recycling industry, explosions can occur due to moisture and contamination in scrap. These explosions, commonly called furnace pops, range in violence and have been known to result in injury and death. Additionally, the destruction of equipment, and plant facilities, not to mention the liabilities, repairs, and downtime expenses.
A cup of water added to 40,000 pounds of molten aluminum can level a 100,000-square-foot area.
What Causes Issues in EPDM, TPO & PVC Roof Systems
Architects and engineers usually specify commercial and industrial roof systems. They're looking for characteristics like chemical resistance when weighing differing types of membrane. However, they're installed by a roofing contractor or subcontractors, warranted by manufacturers, and maintained by building owners or managers.
Every year, billions of dollars in unnecessary costs amass for American businesses in many industries when building issues arise. However, no one takes ultimate responsibility for the performance of the roof system and the intended use for the building.
Many roofers will gladly sell and install a new roof on a commercial/industrial-use building. However, the company installing the roof may not know or understand the true usage aspects of the building. Let alone, the importance of the appropriate roofing system regarding the contents and use of the building.
In over 90% percent of all roofing system integrity failures, the problem is not due to the roof system itself but to:
- Mismatching the roof system type to the specifications of the building type
- Improper installation of the roof system or the insulation system
- The type of adhesives or fasteners
- Failures in flashing, rooftop drainage, skylight, or other roof additions
- Excessive rooftop traffic
- Improper installation or maintenance procedures for rooftop equipment
The manufacturer's warranty covers only about five percent of roof system problems, assuming it is still in effect. What happens when building owners don't comply with warranty requirements, recommendations, and maintenance? It's estimated that nine of ten manufacturer’s roof system warranties are voided before the new roof is 18 months old.
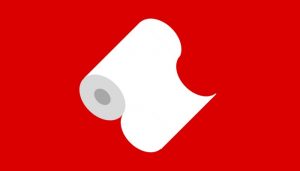
Membrane Industrial Roofing System Design and Installation
Today's thermoplastic roof systems are designed and developed specifically for flat roofs. Popular options include synthetic rubber, ethylene propylene rubber, ethylene propylene diene, and other single-ply materials. The average panels are 18-20 gauge in thickness. Subsequently, non-flat roof adaptations produce areas of weakness in roof systems.
For example, where 97% of roof blow-off begins, a flat roof perimeter-edge wind uplift is typically prevented with a perimeter nailer and a fastener installed three to four inches on center. Pre-engineered steel buildings have no perimeter nailers, nor can they be installed.
A 100,000 sq. ft. area thermoplastic roof requires over 60,000 fastener penetrations. Fastener penetrations that have broken the galvanized finish on the roof panel will begin to rust out completely. From the start of the system installation to reinstallation at the end of the warranty term, a thermoplastic roof will introduce an average of 120,000 penetrations into a 26-gauge metal panel.
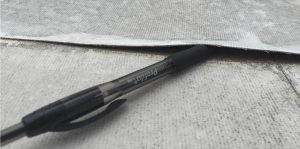
The EPDM, TPO, and PVC roof systems have heat-welded seams. Every 10,000 feet of roof would have approximately 15,000 lineal feet of potential seam failure.
So, if any liquids are used within the building, they will cause condensation between the roof steel panels and thermoplastic membrane and its insulation. Once moisture saturates insulation it renders it useless to control hot and cold temperatures within the building.
Designed and developed to be used on flat roofs with an average panel of 18-20 gauge, the thermoplastic roof is four to five times the weight of the MR Multi-Ply® Roofing System. The extra weight of TPO generates fastener backout, exceeding 1,000-plus pounds per square inch (PSI). 26-gauge material will have difficulty maintaining its hold at 200-400 PSI, well below the strengths the manufacturer developed and designed the system for.
An assembled roof system changes the fire characteristics of an entire facility, increases insurance costs, and increases weight. EPDM, TPO, and PVC roof systems require a structural engineer to recertify any building over 20 years old for weight calculations.
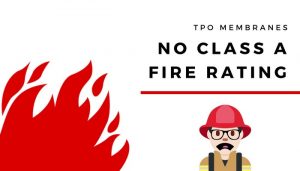
Also, thermoplastic membranes do not have UL or FM wind uplift testing on pre-engineered buildings nor are they able to maintain a Class A fire rating.
MAINTENANCE AND REPAIR OF THERMO-PLASTIC ROOF SYSTEMS
EPDM roofing, TPO, and PVC membranes are highly reflective during installation. This characteristic is commonly associated with energy efficiency. However, it is measured that unwashed roofs in industrial environments will lose 40% of their original reflectivity over a three-year period. Annual washing of the entire roof system is required to maintain reflectivity, all done at an additional cost to the building owner.
The EPDM membrane, TPO, and PVC membrane manufacturer cannot warrant interior gutters unless specific details are followed. Due to the installation process, a roof leak in the gutter forces the repair technician to examine the entire roof, which entails visual and physical manipulation of thousands of feet of field-installed seams and at best, will require multiple trips to the site to discover where water may be entering.
Thermoplastic membranes require highly technical repair, whether the damage is caused by flying debris or even a new penetration through the roof membrane. The thermoplastic roofing system should not be repaired below 40 degrees.
Considering first-quarter and fourth-quarter external temperatures in northern climates, a warranty would then have half its actual length and would be a useless warranty during that time. Even in Midwest states with higher elevations, TPO fails much faster than was anticipated. The MRCA T R committee even issued an advisory on TPO accelerated weathering due to solar or thermal loading.
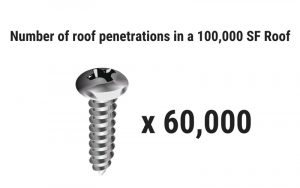
EPDM, TPO, PVC roof systems have no rejuvenation and regeneration properties. They must be completely removed and disposed of at the end of the warranty term. The additional cost to remove and reinstall a new roofing membrane would require another 60,000 new fastener penetrations for an area of 100,000 square feet.
Additional insulation required to install a membrane will not show a return on investment for approximately 12-15 years when the typical Thermoplastic roofing system warranty is no longer available.
Lastly, an EPDM, TPO, PVC roof system must be depreciated over 39 ½ years for tax purposes. Multi-Ply Roof Systems are 100% tax deductible the first year.