RCI Interface Featured Article: Why You Should Think Twice About Putting a Single-Ply Roof on a Metal Building
Originally posted November 30, 2016 By RCI Publications - By Charlie Smith and Terence E Wolfe PE.
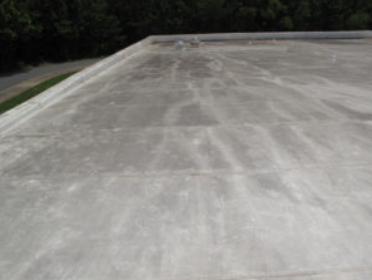
Figure 1 - This low-slope metal building with a trapezoidal standing seam was re-covered with a single-ply membrane. Water tends to flow in the deflection mid-span on the purlins. The use of single-ply membranes to re-cover existing metal roofs on metal buildings has become very popular over the past several years. It’s fast, it’s easy, you can get a warranty, and it’s relatively inexpensive. There are millions of square feet done every year. Most people involved in this activity are not aware of the increased risk this causes for
themselves and the building occupants. Simply said, a pre-engineered metal building is not designed to have a single-ply roof on it.
A building that is designed to have a single-ply membrane roof system will be
supported by bar joists. Bar joists are not connected to each other from bay to bay, and act independently of each other. Moreover, bar joists have built-in camber and create a level surface once they are attached to the main frames and dead loads are applied. This surface works great for a membrane roof
application because the water flows equally across the entire roof surface.
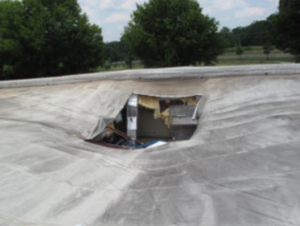
Figure 2 - This same building roof collapsed due to several factors related to a single-ply re-cover.
In contrast, a metal roof on a pre-engineered metal building is attached directly to C- or Z-shaped purlins, which are, in turn, lapped and connected to each other over the top of each rafter frame. Rafter frames are typically 25 feet apart. Purlins are produced completely level and are designed to have a dip or deflection between frames once they are installed. Equal loading across each purlin is critical to the design of a metal building; and since the purlins are connected to each other, what happens in one bay will affect the adjacent bays. Furthermore, many pre-engineered metal buildings that are standing today are designed for balanced loading across the entire structure. The assumption is the load on a building would be uniform; thus, the purlins in one bay will not get pushed down or deflected more than the adjacent bays.
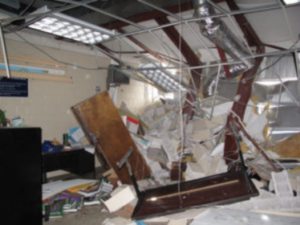
Figure 3 - Interior shot of collapse. When there is a ribbed metal roof in place, water flows down between the ribs of individual panels to the gutter. This ensures equal loading on the purlins and confinement of that water to an individual bay. If one chooses to recover a low-sloped, metal roof on a metal building using single-ply membranes, the water flow is changed. Since there are no ribs to confine the flow as the water moves downslope to the gutter, the water will naturally flow towards the mid-span of the purlins where maximum deflection occurs. This can be seen clearly in Figure 1.
On lower-slope structures with a metal roof in place, if there are any dips or low spots caused by a wide-span bay, a damaged or overloaded purlin, or damaged roof panels, the water may pond locally but stays within the confines of the individual panels. With a single-ply membrane in place, localized ponding over a
weak purlin will grow over time because the water flow within the entire bay will be drawn toward it every time it rains. As the dip accumulates more and more water and forces the weak purlin down in the affected bay, the purlins in the two adjacent bays will rise. Eventually, this can divert water from adjacent bays into
the affected bay. The result can be catastrophic, as shown in Figure 2, a photograph of a school with an internally drained trapezoidal standing-seam roof that was retrofitted with a mechanically attached single-ply membrane.
There are several ways this can happen with a single-ply re-cover, such as in the following scenarios:
1. An overloaded or damaged purlin that ponds water to start with. Building occupants hang all kinds of things from the purlins in metal buildings with little regard for or understanding of the capacity of that purlin to handle additional weight.
2. A dip in the panels between the eave strut and the first purlin. This is where you are most likely to see ponding water on a metal building roof. It is normally due to poor installation practices or too much foot traffic, such as maintenance personnel accessing the same roof location every time.
3. A sudden surge of water laterally from one bay across into another. This can be the result of the billowing effect of a mechanically attached single-ply membrane under high wind loads. Negative wind pressure lifts the area between the seams of a single-ply roof like a balloon. The risen part on
each sheet moves rapidly across the roof, displacing water as it goes. On a metal building, water could easily get displaced from several bays across into one bay in a matter of seconds with this billowing effect. Watch the video on the following link to see a single ply billowing and pushing water during a strong thunderstorm recently: https://youtu.be/5LUlX9aNr80. In the video, this is happening along the outside edge of the building that is exposed to the wind. Can you imagine what this would look like on a wide-open roof that is not protected by a 20-story building like this one is?
4. A clogged scupper or drainpipe. During a single-ply retrofit of the building in Figure 3, the internal gutters were filled, and scuppers were added to handle the water flow out of the parapet wall. This is a very common practice when re-covering existing internally drained metal buildings, and it creates the worst possible scenario on a metal building structure. A clogged scupper outlet caused the initial backup of water onto the first purlin up from the eave in the widest-span bay. As the first purlin was being pushed
down or deflected with the additional weight of the water, the purlins in the adjacent from the two adjacent bays into the wider span bay where the low spot occurred. It also prevented water from reaching the overflow and adjacent scuppers because the eave strut had not deflected along the parapet wall. As a result, it took a matter of minutes for the roof to collapse.
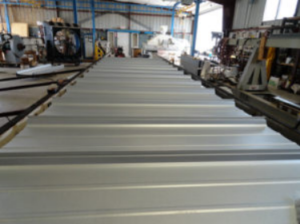
Figure 4 - Roof panels mounted on purlins prior to base testing. A couple of years ago, we did some base testing to determine what effect doing metal-over-metal retrofit had on purlin strength. A base test is where you take two full-length purlins in a single-span condition, with a metal roof attached to them, and push down on the purlins until they buckle. The first test was done over a typical low-slope metal building installation: 8-in.-tall by 16-gauge by 25-ft. long purlins with a 24-gauge, 3-in. by 24-in. trapezoidal standing-seam roof to establish a baseline for the retrofit tests. (See Figures 4 and 5.) Without the retrofit, the purlin buckled at 23.9 psf. One inch of water weighs 5.2 pounds per square foot. That means in this case, the purlin would have failed with 4.6 inches of water on it.
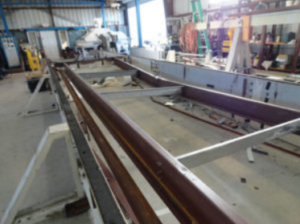
Figure 5 - Purlins after base test failed at 23.5 psf. It would not be hard to imagine 4 to 5 inches of water accumulating on a low-sloped metal building with a single-ply roof on it—especially one that was designed with a gutter that had been altered with crickets to drain out of scuppers.
There are many positive arguments for re-covering an existing metal building roof that is not performing. The trick is to do it in such a way as to eliminate the reasons the roof is not performing to start with. The bottom line is: The best way to recover an existing metal roof on a metal building is to use another metal roof. A metal-over-metal re-cover can be done with minimal disruption to the occupants and within the guidelines of the International Building Code (IBC). Insulation may be added and wind-load capacity can be enhanced without altering the structural diaphragm.
The metal roof system that gives the best chance for success at re-cover is a symmetrical, site-formed, structural standing-seam system. These two-piece systems have the most watertight seam design, provide unmatched wind uplift capacity without additional costly corner or edge zone framing, eliminate leaking end lap joints, and allow for individual panel replacement. The ability to easily repair or remove and replace individual panels on a metal roof has been the missing piece of the puzzle for most building owners.
There are at least five ways to re-cover a metal roof on a metal building with a symmetrical standing-seam system. Several of these methods will actually increase the load-carrying capacity of the underlying purlins at the same time. Most importantly, all five methods help maintain the balanced condition for which
the metal building was originally designed.
Authors:
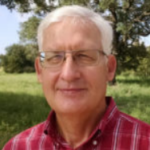
Charlie Smith founded Architectural Building Components in 1989. Over the next 23 years, the company grew into an industry-leading metal roofing and wall system company. In 2012, the business became a part of McElroy Metal, enabling Smith to focus on educational and product development efforts. Charlie
holds several patents in the re-cover field. As a widely recognized metal roofing authority, Smith helped to write the new RCI Metal Roofing course and is a frequent presenter at industry events.
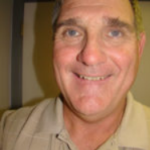
Terence E. Wolfe, PE left MBCI in December 2000 to start Force Engineering and Testing, Inc. As an engineering consultant and certified test lab, his firm is a source in the development of metal roofing systems and re-cover applications for the metal roofing and metal building industry. As the first chairman of the Metal Roofing Systems Technical Committee, he was a primary author of the first edition of the
Metal Building Manufacturers Association’s MBMA Design Manual for metal roofing systems.